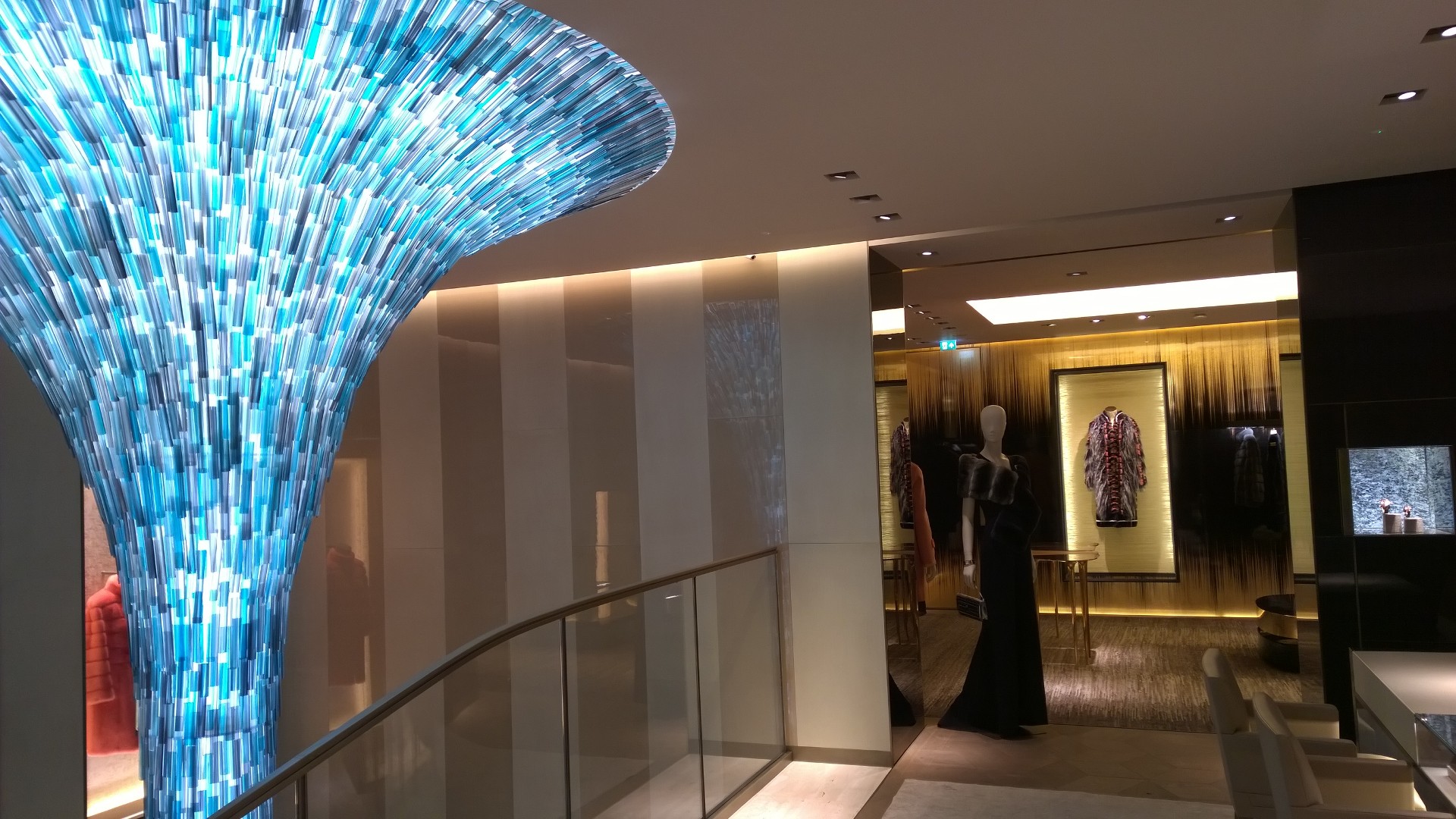
13 Jun CHANDELIER: A NEVER-REALIZED PROJECT COMES TO LIFE
When the request came, I accepted without even seeing the details.
It was 2013 and the fashion label Fendi, of which we were already suppliers, asked me for a work that, until then, had never been realized.
It consisted of a suspended chandelier, almost seven meters high and intended for the stairway of the Parisian boutique of Avenue Montaigne. It was a colossal work, yes, but so was my desire to try out an innovative project.
THE GLASS FLOATING IN THE AIR
“I like the glass floating in the air”, Gwenael Nicolas told me. And the glass that seems to float in the air soon became the leitmotif of all the work we did.
Gwenael Nicolas, this is the prestigious name of the founder, president and art director of Studio Curiosity in Tokyo, would have been our interlocutor, commissioned by the label, for the project.
The desire was to get a chandelier in which each glass was independent and suspended through invisible wires that turned it into a multicolor burst of water frozen in a perfect instant.
It was not only a glass work but also engineering, since its large size, the need to incorporate the lighting system and, ultimately, the necessary provision for a movable section that would allow maintenance works made it complex and involved the work of different professionals.
Initially I contacted Paolo Donà, master glassmaker of Murano who shared with me the passion for challenges, and Ivan Mazzero who joined us, then, from an engineering point of view.
The real challenge, in fact, was that the glass coverslips that would make up the chandelier, like the plumage of a parrot, had to remain suspended in the air without the supporting structure being seen.
We started testing to create samples for Gwenael.
The first attempt failed, and others followed: five. In the attempts to materialize that idea, however, Gwenael’s criticism was always constructive. We were all rowing in the same direction.
It was not easy to find a way to hang 3900 glasses with 6500 holes, using 6.5 km of nylon wire with as many fasteners, and also create the slender support structure capable of supporting the 380 kg of the chandelier.
THE RIGHT PROTOTYPE
We arrived at the fifth prototype of a 1:1 scale section 1 meter high that we presented at the European Institute of Design in Milan and that represented a slice of the upper part of the work. In looking for the invisible system to hang the glass tongues we had gone from the nylon thread sewn and fixed with plastic screws to finally arrive at the nylon thread no longer sewn but that supported each single glass.
This prototype turned out to be the right one and so we moved on to engineering the work.
This had to include the lighting system, created by a lighting designer in New York, which predicted that the lights could enter from above inside the chandelier and that a motorized part allowed the maintenance.
We made a motor mounted on a rotating shaft that made the whole upper cup of the chandelier fall on itself for one meter, with a telescope, allowing access.
It was time to produce the glass tongues. The designer wanted the colour to be nuanced but with an absolutely particular and difficult to execute nuance.
Paolo Donà, an expert in the production of hand-drawn Murano glass, created and suggested to the master Murano glassmaker the method for making it.
The invisible structure that we finally created was to attach the glass tongues with a wire above and below in the points where the design of the work curved and with a wire only above in the points perpendicular to the ground. We also created a three-dimensional template almost 7 meters long to reproduce, in the laboratory, the assembly and its process.
The design phase that started with the various prototypes and ended with the assembly test lasted three months.
The entire upright structure was transparent, except for a small steel tube. The transparent polycarbonate contained the lights that went down from top to bottom and the nylon wire fastening sectors positioned at a distance of one meter from each other.
THE TRIP TO PARIS
We only had to go to Paris to set up the final work. With a team of four we set out and started to install the chandelier from the bottom up so that the glass slightly overlapped each other. It was a month of hard and uninterrupted work. There were some difficulties, yes, but we got over them and the managing director of the house and Gwenael Nicolas came personally to compliment us for what we had achieved.
It was a complex work and – in the manner of Benvenuto – full of trials and attempts. An award-winning achievement, not only from the pride of having created a unique work, but also from the recognition of the label.
In 2014, another chandelier of our brand of the same type but bigger, 10 meters high and with even more complex engineering solutions, enriched the house’s flagship store on New Bond Street in London.
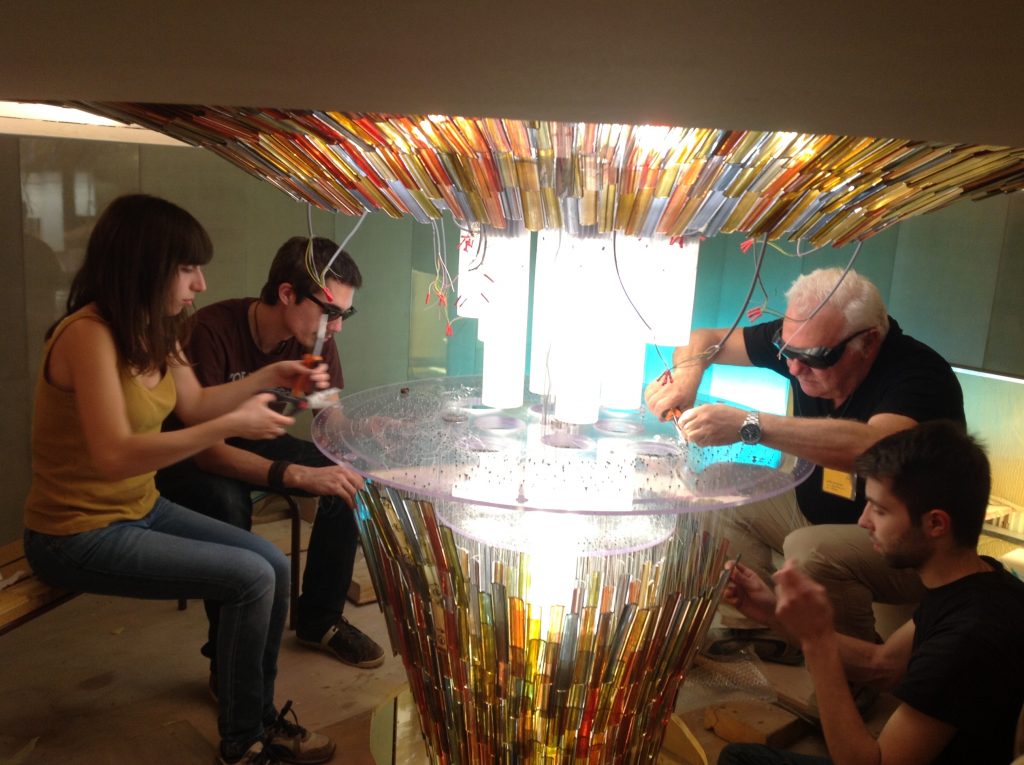
“The artistic and constructive challenge was very hard, but these are the challenges that fuel our daily passion for creating something that previously found place only in the imagination.”
Vittorio Benvenuto