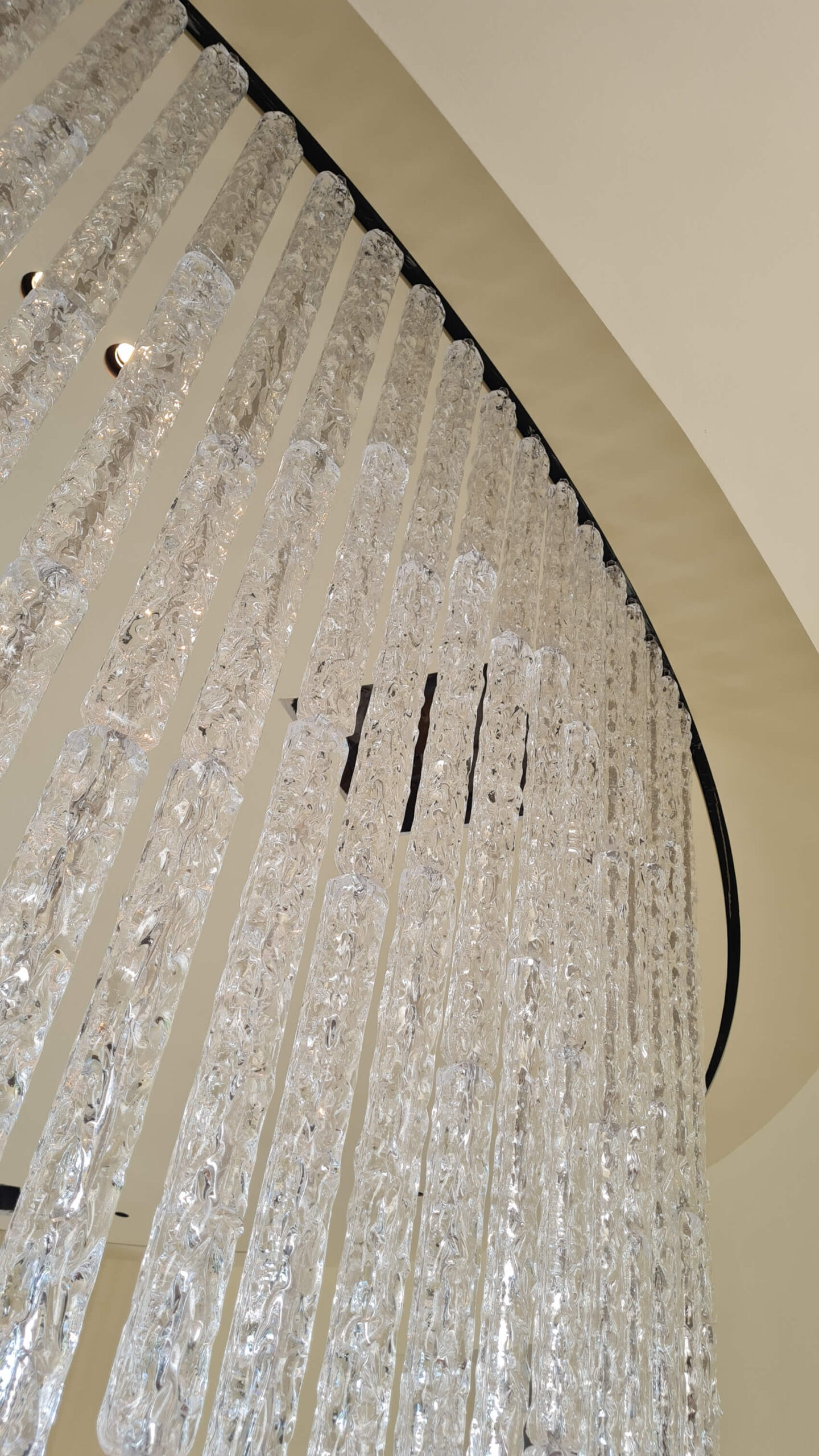
13 Jun CAST-GLASS BETWEEN CRAFTSMANSHIP AND ATTENTION TO DETAIL.
THE PROJECT FOR THE SALON MARTEL IN PARIS.
Salon Martel, a luxury leather goods retail in Paris, is now close to opening on rue François 1er. Alexandra Martel, the owner, is a young woman very attentive to detail and her creations, also thanks to ultra-technological machines, are finished to a high standard that easily competes with that of the major fashion houses that make the French city the capital of the sector.
The brand follows a pseudo-ethical path that, while working with leather, is oriented to use without waste. Although for a bag, for example, the exact point of the leather to be used is identified, the rest, as well as being used for details such as handles and small leather goods, is ultimately sent to schools so that students can experiment during teaching workshops.
In 2024, the Voltaire studio, an architectural firm that had known me for my work for the LVMH Group, commissioned me to produce samples of furniture for the Salon. These were two slightly arched sliding walls that would be mounted in an area of the boutique.
The project envisaged that the walls, not more than one meter and sixty centimeters wide, were composed of seventeen glass columns on each side, three meters and thirty tall and very thin. These were to be made of glass and would contain inside them a stainless steel core as its axis. To construct the columns, cast glass pieces are arranged in various sizes, ranging from thirty-eight to seventy centimeters. In addition, the track on which the walls would be mounted was to be electrified so that they could be opened and closed automatically.
In the design and sampling phase, we decided to make the columns in pieces, given the height, and in two half shells to be joined during assembly.
As Benvenuto Mastri Vetrai I do not deal internally with cast glass, and so I contacted the Vetreria San Giuseppe of Piombino Dese that supported me in the realization of samples, first, and the order, then.
In the sampling phase, the customer requested several prototypes: crystal, crystal with bubbles, light amber and other colors. It took several months and several tests, of glass itself and of assembled glass, to arrive at the final choice that saw leaning towards a transparent crystal with bubbles and very corrugated and plastic surface. Towards the end of February 2025, we produced a full-size column mock-up.
The presence of bubbles in the crystal is not natural and, for this reason, if commissioned, it must be created specifically. The danger is that too many or too few bubbles or even unsightly shadows will be created. The glass is poured by hand by expert glassmakers, but it remains a manual activity and therefore characterized by craftsmanship. To create the final bubbles, from one to three millimeters in diameter each, the glass was poured wire so that it trapped air inside, but the mould has been modified several times to obtain that of the right shape and also the choice of glass has been tested, from harder glass to changing the temperature in which it is poured, to the object used to pour it, ladle or iron.
The sampling and study process turned out to be a training opportunity to guarantee that all glass pieces were handled in the identical manner.
After a few months, I had the opportunity to meet the client personally in Paris. Endowed with a great aesthetic taste she is also a person of absolute precision, which reflected his character even in the requests related to the contract. But in craft glass it is difficult to reproduce by hand with the same precision in millimetre terms. The issue was resolved with an invitation for a visit to the furnace, on the occasion of the last samples, in which the customer could see with his own eyes how we were proceeding with the work. Fascinated by the casting of incandescent glass she has better understood how the work is made and, after a last sampling, confirmed for production and subsequent installation, which took place just these days in Paris.
The installation on the curved sliding track included holes nine centimeters apart that would allow the fixing, one by one, of the columns. The glass column would have left uncovered the last six, seven centimeters above where there was a thread that allowed it to lock. In addition, to anchor them to the base I curved a stainless steel plate two centimeters thick and three wide with all the holes corresponding to those of the upper track, where the steel column could be blocked preventing oscillation to movement.
The last thing to do was fly to Paris to put our creation into action and make sure everything worked properly.
A work, even if it is cared for in the smallest details, as in this case, always hides an aura of uncertainty that will be dispelled only with the final installation. Only at the end we can really say that we have succeeded in giving shape to the idea.
And we had this certainty at the end of the installation, not without difficulty, from the radiant expression of happiness of Alexandra when she saw for the first time the completed work.