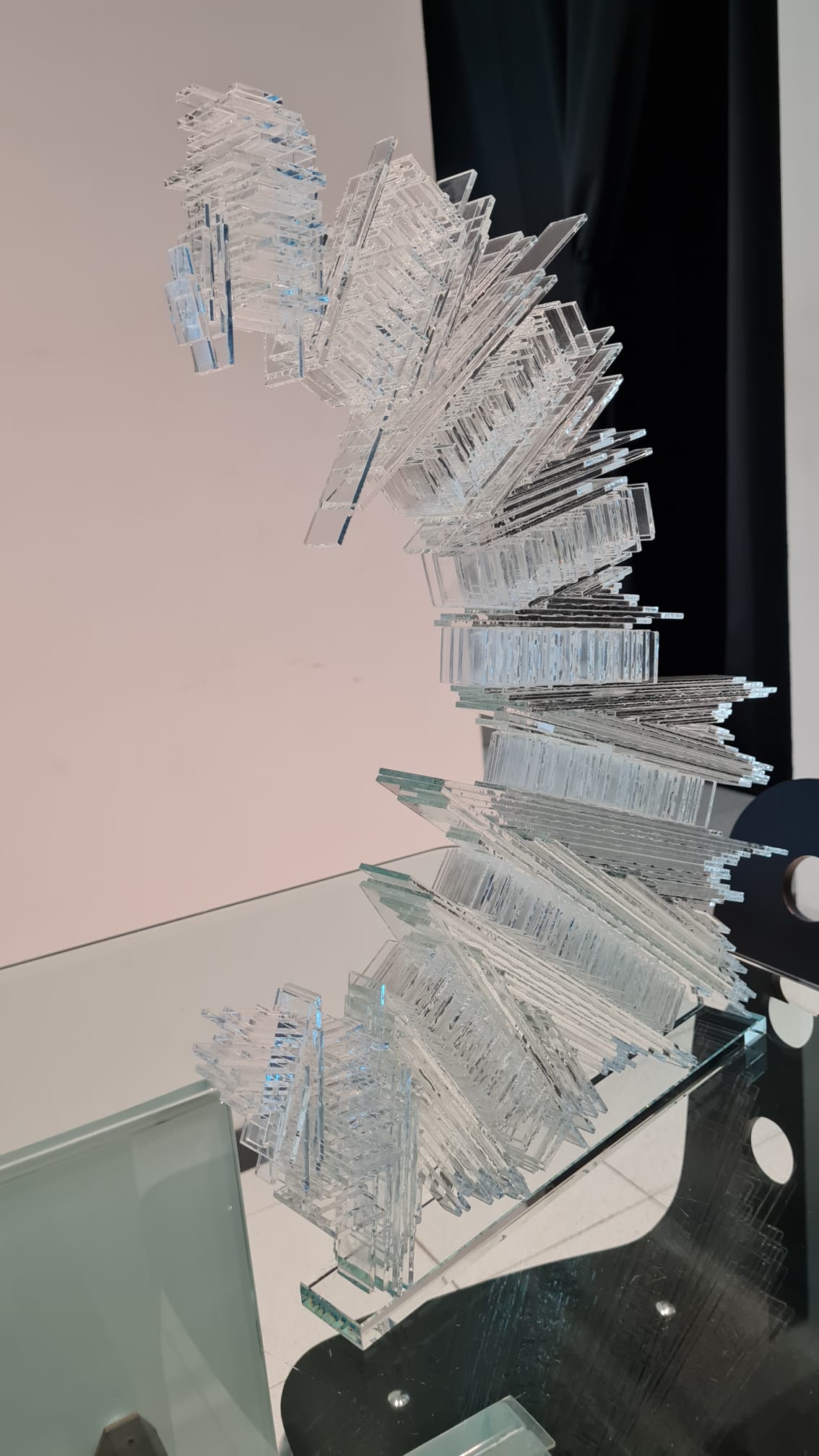
22 Apr BAROVIER ART: A LAYERED GLASS SCULPTURE PART OF A VERY VARIED HISTORY OF WORKS
In Fondamenta dei Vetrai, on the banks of the homonymous Venetian river, stands the Barovier&Toso, one of the most famous furnaces of Murano and also one of the oldest companies in the world with its seven hundred years of history.
In 2015, the company Barovier&Toso was bought by Rinaldo Invernizzi who, besides being a businessman, is also an artist. Invernizzi commissioned me some samples. Specifically, we experimented with the fusions of the cotisso, known as Murano glass blocks.
Until, in 2024, the company asked me for a glass reproduction of a sculpture originally made by an important oriental artist. The latter had provided both sketches and a 1:1 scale cardboard model. The sculpture was not large, it measured about fifty centimeters, but it consisted of several glass plates glued in a curved way.
To the request I answered yes, as usual, without assessing thoroughly the difficulties; since these are overcome as they come.
So, from Venice, the model arrived. The first thing I thought was: “Will the UV hardening resin, on such a small surface, be able to maintain such an unbalanced structure?”It was, in fact, a kind of half spiral very unbalanced.
Its surfaces, fixed one after the other, would have added resistance, but at certain points of leverage the weight would have been greater.
We decided to try building it in blocks.
In total, there were about five hundred and thirty pieces of glass to be glued with UV resin in a way, however, very particular and difficult in the field of glassware.
The sculpture had a curved shape and, right at the point of curvature, the glass surface that had to be glued was gradually smaller, which generated an imbalance and the possibility that the work could break at any time, just a matter of weights and inclinations.
I contacted Barbara, a friend who could take care of the gluing of glass, and we got down to work.
The artist had sent us an excel table with the list of all the glasses and their dimensions in millimeters, divided by measure, with which we proceeded to cut. Then it was the turn of the grinding to remove the cut and then we started gluing.
On a very large table we placed the material and Barbara began.
About halfway through work I realized that there was too much space between one glass and the other in the bonding phase – the UV resin must be pressed well because it makes thickness -. So, it was necessary to make some adjustments.
At the end of this phase, we realized another difficulty: to make it stand alone. The base was small and wobbly.
We created a base with a quite thick rectangular glass – as wide as the largest glass of the sculpture and about thirty centimeters long – in order to give stability to the structure. The modification was approved by the artist. We straightened it with a grinding, on a diamond plate, with water to flatten and increase the gluing surface and make it firmer.
Finally, we glued the second half of the structure which was also the most critical.
It came out well. But the difficulties had not all been overcome. The next problem was the packaging, for which I opted for polyurethane foam and a wooden case. Shipped! When the sculpture arrived at Palazzo Barovier&Toso in Murano, where an exhibition on several floors with furnished rooms had been made, they called me to tell me that it was detached right on the middle. We went there to fix it and, at that point, a case was also requested to protect the sculpture. In fact, it had been placed between two very large sofas on a corner shelf, black and glossy. Beautiful! And of great effect also thanks to the very scenic lighting that emphasized its shape. Glass bonding is a delicate technique. As long as the glasses are overlapped there is no problem, but when they are pointed to create a curvature, the bonding surface is very little and you rely only on the strength of the glue.
UV resins are families of resins which are classified according to density and resistance. In the realization of this work, we opted for a type of UV resin more liquid for the bonding glass to glass – which did not give thickness – and for a second type of a thicker UV resin for the reinforcement of the most critical points.
The history of laminated glass works is very diverse. It’s not a new thing. Since this possibility of gluing with a transparent glue was born, which remains so over time, both artists and craftsmen had a field day.
Vittorio Benvenuto